Battery Charge Controller
Charge Controllers For A Longer Battery Life
For many people, building their own solar panel system and living off-grid is becoming a reality instead of a dream. Connecting the solar panels directly to a single battery or bank of batteries for charging may work, but is not a good idea. What’s needed is a battery charge controller to safely charge and discharge your deep cycle battery for a longer lifespan.
A standard 12 volt solar panel which can be used to recharge a battery, could actually be putting out nearly 20 volts at full sun, much more voltage than the battery needs. This difference in voltage between the required 12 volts need for the battery and actual 20 volts being generated by the solar panel translates into a greater current flow into the battery.
This results in too much unregulated solar generated current overcharging the battery which could cause the electrolyte solution within the batteries to overheat and evaporate off, resulting in a much shortened battery life and ultimately, complete battery failure.
Then the quality of the charging current will directly affect the life of any connected deep cycle battery, so it is extremely important to protect batteries of a solar charging system from being overcharged, or even undercharged, and we can do just that using a battery charge regulation device called a Battery Charge Controller.
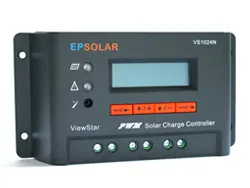
A battery charge controller, also known as a battery voltage regulator, is an electronic device used in off-grid systems and grid-tie systems with battery backup. The charge controller regulates the constantly changing output voltage and current from a solar panel due the angle of the sun and matches it too the needs of the batteries being charged.
The charge controller does this by controlling the flow of electrical power from the charging source to the battery at a relatively constant and controlled value.
Thus maintaining the battery at its highest possible state of charge while protecting it from being overcharged by the source and from becoming over-discharged by the connected load. Since batteries like a steady charge within a relatively narrow range, the fluctuations in output voltage and current must be tightly controlled.
Solar Battery Charge Controller
Then the most important functions of battery charge controllers used in an alternative energy system are:
- Prevents Battery Over-charging: This is too limit the energy supplied to the battery by the charging device when the battery becomes fully charged.
- Prevents Battery Over-discharging: Automatically disconnect the battery from its electrical loads when the battery reaches a low state of charge.
- Provides Load Control Functions: Automatically connect and disconnect the electrical load at a specified time, for example operating a lighting load from sunset to sunrise.
Solar panels produce direct or DC current, meaning the solar electricity generated by the photovoltaic panels flows in only one direction only. So in order to charge a battery, a solar panel must be at a higher voltage than the battery being charged. In other words, the voltage of the panel must be greater than the opposing voltage of the battery under charge, in order to produce a positive current flow into the battery.
When using alternative energy sources such as solar panels, wind turbines and even hydro generators, you will get fluctuations in output power. A charge controller is normally placed between the charging device and the battery bank and monitors the incoming voltage from these charging devices regulating the amount of DC electricity flowing from the power source to the batteries, a DC motor, or a DC pump.
The charge controller turns-off the circuit current when the batteries are fully charged and their terminal voltage is above a certain value, usually about 14.2 Volts for a 12 volt battery. This protects the batteries from damage because it doesn’t allow them to become over-charged which would lower the life of expensive batteries. To ensure proper charging of the battery, the regulator maintains knowledge of the state of charge (SoC) of the battery. This state of charge is estimated based on the actual voltage of the battery.
During periods of below average insolation and/or during periods of excessive electrical load usage, the energy produced by the photovoltaic panel may not be sufficient enough to keep the battery fully recharged.
When the batteries terminal voltage starts to drop below a certain value, usually about 11.5 Volts, the controller closes the circuit to allow current from the charging device to recharge the battery bank again.
In most cases a charge controller is an essential requirement in any stand-alone PV system and should be sized according to the voltages and currents expected during normal operation. Understanding your batteries and their charging requirements is also a must for any battery based solar system.
Any battery charge controller must be compatible with both the voltage of the battery bank and the rated amperage of the charging device system. But it must also be sized to handle expected peak or surge conditions from the generating source or required by the electrical loads that may be connected to the controller.
There are some very sophisticated charge controllers available today. Advanced charge controllers use pulse-width modulation, or PWM. Pulse width modulation is a process that ensures efficient charging and long battery life. However, the more advanced and expensive controllers use maximum power point tracking, or MPPT.
Maximum power point tracking maximises the charging amps into the battery by lowering the output voltage allowing them to easily adapt to different battery and solar panel combinations such as 24v, 36v, 48v, etc. These controllers use DC-DC converters to match the voltage and use digital circuitry to measure actual parameters many times a second to adjust the output current accordingly. Most MPPT solar panel controllers come with digital displays and built-in computer interfaces for better monitoring and control.
Choosing the Right Solar Charge Controller
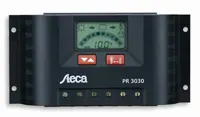
We have seen that the primary function of a Battery Charge Controller is to regulate the power passing from the generating device, be it a solar panel or wind turbine to the batteries. They assist in properly maintaining the solar power system batteries by preventing them from being overcharged or undercharged, thus offering long life to batteries.
The solar current being regulated by a battery charge controller not only charges batteries but can also be passed to inverters for converting the direct DC current to alternating AC current to supply the utility grid.
For many people who want to live “off grid”, a charge controller is a valuable piece of equipment as part of a solar panel or wind turbine power system. You will find numerous charge controllers manufactures online, but choosing the right one can sometimes be quite confusing and to add to your worries they are not cheap either, so finding a good quality solar charge regulator really matters.
It’s best not to go for those low quality cheaper ones, as they may actually harm the battery life and increase your overall expense in the long run. For a little peace of mind, why not check out some of the Renogy battery charge controllers available from Amazon and learn more about the different types of solar charge controllers available as part of your solar power system helping you to save money and the environment.
Hi. Im considering a combination of wind and solar power generation for my boat kept on mooring. I think a combination would be good as Scotland not blessed with lots of sun and my mooring is a bit sheltered with harbour wall. Can i plug output from 2amp wind turbine into a Renogy mppt regulator (20 amp), would it manage the power to my batteries in same way as with a solar panel?
MPPT controllers have been used for photovoltaic (solar) power for a long time, but can also be used for wind turbines. In real life the wind speed is not constant, but changes continuously, thus the ideal rotor RPM for maximum torque will also change. What is important to remember is that there is an optimum RPM for each wind speed, and that is where we want to run the wind turbine to achieve MPPT.
However, to work properly the controller needs an MPPT power curve that is specific for the wind turbine that you want to hook up to the controller. So check the MPPT’s manual if you can connect it to a wind turbine. If not, then it is not advisable since unlike PV, a wind turbine can output much higher open circuit input voltages (Voc) when it is not loaded up or your batteries are full.
I have a 730 W, 76 V solar panels system charging 24 V battery set up using a Morning Star MPPT charge controller in an OFF GRID set up. Which is the best suited APC or LUMINOUS UPS/Inverter that is solar compatible that can be used.
Hello, I have read your site with interest. We have a large dwelling with a business operating from it. Our standing load without all onsite is around 4KW This is a combination of servers and IT equipment, freezers, fridges etc. When all onsite with heating lighting TV’s etc. this can reach 10+KW our energy costs are spiralling out of control.
We have a large paddock approx 50m from the nearest 240V electrical connection into the site wiring that is in a barn.
We are looking at taking a step into solar. Our initial aim is to simply power the office load using purely solar Generated energy whenever it is operating and obviously use the grid for any shortfall. We know the property will consume all of the power generated.
We had a couple of thoughts.
1) Simple system. Setup an array that can generate approx 3KW and connect it to a Solar inverter and simply connect that into the property wiring system as an input.
Whatever it produces should be consumed first before we need to get energy from the grid. Is this assumption correct assuming we have a local load at or exceeding the solar-generated capacity?
2) As an expansion of 1) above. We would look to build a larger array and connect that to a battery bank (this looks like the black magic area) that has enough capacity to provide a stable supply to an inverter that would then be connected as before into the property wiring systems that would provide a variable load of between 4 and 10+KW we have seen peaks of 12KW on our monitor that is clamped onto the incoming 100A 240V Grid connection.
How would we size the array and battery system and corresponding Invertor etc.
Are higher voltage panels better than lower voltage panels?
Are higher string voltages better than lower voltages from a power conversion point of view. e.g. is it more efficient to convert from 48V to 240V rather than 12 or 24V to 240V
If I have a string of 24V 1000Ah made up of a series connected 2 x parallel 12V strings of 5 x 12V 200Ah batteries giving me 24V 1000Ah of capacity or in theory 24KWh what size inverter would I need to provide power into the property and would my system use the power I have before going to the grid?
I am sure some of these questions are a bit basic but we are very DIY-orientated people and want to build this ourselves. Any help in understanding this would be great. I am sure there is much left out of my note. Like cable sizing etc.
Logically I think we know what we think is happening, but, that doesn’t make it so! Like will we consume all we have before taking anything from the grid? I apologise for any typos or grammer.
Cheers
Tony
There are a number of good points raised here, and we will attempt to answer them. Firstly, an inverter fed grid-connected, or grid-tied system is basically a bunch of solar panels (or turbines) connected to a single inverter (or a collection of small inverters) feeding power directly to the utility grid. Generally, PV inverters operate as current sources injecting electric current into the utility grid in-phase with the grid voltage.
It is commonly assumed that ALL the power generated by the PV panels (array) is consumed at the point of generation but this is not always the case. Power consumed is both active (real) and reactive. PV panels generate active power only. If your average power consumption is, for example, 10kWh per day, and you generate 12kWh for the 4 hours of full sun that day, then some of the inverters output power maybe autoconsumed and some may flow into the utility grid. Equally 100% inverter current may flow into the grid and you may consume 100% from the grid, just slowing down your energy meter in the process.
On average PV panels generate maximum power for 4 to 5 hours of full sun per day as they do not consistently generate power 24 hours per day at their nominal output wattage rating. Oversizing an inverter by having more DC input power than the inverters AC output power, may increase power output in lower light conditions, thus extending the 5 hours. As would solar tracking. Connecting a battery bank would allow for more autonomy but at a cost and an increased array size, as now the array has to charge batteries for 5 hours plus feed the grid. Then the size and type of grid-connected system would ultimately depend on how many hours of autonomy you require and how much you are willing to pay upfront.
Higher string voltages are better providing everything stays within tolerance at worst case conditions. As P = V*I, a higher voltage (V) means a lower current (I) for a given power (P) and therefore smaller diameter cabling so cheaper. PV panel voltage depends on the wattage (100W or 400W) of the panel. Higher PV wattages means physically bigger panels, which means more m2 of installation area.
the article states the controller should stop charging a 12V battery at approx 14.2V, what about 6 volt batteries – same?
No of course not. A single 3-cell 6 volt rechargeable battery should have a fully charged terminal voltage of about 6.35 volts. To correctly charge a wet battery, the output voltage of the charging system needs to be slightly higher than the batteries fully charged terminal voltage, to ensure that the charging current flows in the direction from charger to battery. A constant voltage equal to between 2.35 to 2.45 volts per cell is recommended for charging storage batteries. Thus for a 12 volt, 6-cell battery this is between 14.1 and 14.7 volts, so the charge controller should stop charging the battery once this voltage level is reached, or switch to a low current float charge. For a 6 volt, 3-cell battery this voltage level is between 7.05 and 7.35 volts.
Very nice article, totally what I needed.
Clarity please, since we have ; flooded batteries, sealed and gel. Under which category do the “gel hybrid agm batteries” fall? Thank you
Flooded or wet type batteries are your typical lead-acid batteries which have a liquid electrolyte solution of water and sulfuric acid. They have removable caps for charging, maintenance and topping up with distilled water. The electrolytic solution is highly corrosive and they must be kept upright at all times.
AGM (Absorbed Glass Mat) batteries are valve regulated lead acid batteries which are fully sealed and have one-way pressure-relief valves fitted into their case so can be titlted. Excessive gas build-up due to overcharging or cell failure can escape through the pressure relief valves. The electrolyte in AGM batteries is completely absorbed in separators consisting of matted glass fibers between the electrodes and are promoted as being maintenance free for life.
Gel batteries are another type of sealed battery which do not have a liquid electrolyte but a thick semi-solid silica gel type substance with no water. Because gel batteries have no removable caps or vents they are considered to be fully-sealed, non-spillable and maintenance free, thus unlike flooded batteries, gel batteries can be placed and installed upright or on their sides in racks as part of a renewable energy storage system.
“Hybrid” Gel battery is a marketing term and not a real battery technology.
I have a 6V 4.5mAh fan.
What size of solar panel do i need to charge it effectively, if direct.
Secondly, if with charge controller
Electrical Power (P) = Volts (V) times Amps (A), thus P = V*I = 6*0.0045 = 27mW. So the lowest wattage 6 volt panel you can find would power your DC fan.
At what point can we know that a battery is fully charged? Is it when the solar controller reads 14.2v and the arrow at the left hand side of the solar control stop flashing? Pls reply
This is an unusual question. Clearly if your charge controller or user manual is telling you that the battery is fully charged, then it must be.
I am planning on installing an off grid solar battery system using lead acid batteries. I currently have 22 solar panels installed connected to the grid. It is my intention to remove the grid inverter and install a Sunnyboy Island inverter, a power controller and a bank of lead acid batteries.
Could I receive advice on the best size and model power controller I will need to set up this system. If possible could I receive advice on the number of 12 volt lead acid deep cycle batteries I will need for a load of approximately 20 amps.
Hi David,
On the looks of your question my first thoughts are that you are new to harvesting solar power or I could be completely wrong. To begin with, your question consists of 2 parts.
First one being the power generated from the panels installed and second being the controlled discharge of power from batteries. I’m assuming that you are aware of the different panel specifications and how you have wired them to get your desired voltage. There are controllers available in 12, 24, 36 and 72 volts capacity.
Coming to discharge part (the inverter), 20 amps of current is quite a high number. You can use a single deep cycle battery (remember to buy a battery with a minimum 20C capacity) or connect them in parallel, but it is recommended to split the load on many batteries for them to last longer. Also remember that batteries with higher ‘C’ value are more expensive.
I could help you with precise number of batteries and controllers if you tell me the specifications of the panels and the wiring method.
I hope I answered your question.
I have got Hulikkar Battery Bicycle(Medlay) 26″. I like to add Solar Panel with Bicycle and controllable with this cycle. Is it available with you and its price. Do you send it to cash on delivery and how many days it will take.
Thanks,
Your Sincerely,
SUDERSHAN GOSAIN
H.NO 87 KESAR BAGH COLONY, NEAR N.I.S.
PATIALA, PUNJAB
I have purchased sixteen 12-volt deep cycle batteries, each with 134 amp-hours @ 20 hr rate. I plan to wire two sets of 8 batteries each in parallel to increase my amp-hour capacity, and then to wire these sets together in series to increase the voltage to 24 volts.
My question: Can I still charge this bank of batteries with my 12-volt windturbine, my 12-volt solar panels, and my 12-volt battery charger?
Many thanks for your comments.
Hal Nash
My project will use a 300W solar panel to supply power to a 50W load and a 250W pump. The PV will will run through a regulator to a battery. The power will go from the battery to DC/AC Inverter. The AC will then power the load and the pump. The pump will take water from a 55 gal drum (A) and cycle it to another 55 gal drum (B).
When the battery power drops below 12.1V a valve will open in drum B and take the water to to a turgo runner connected to an alternator. The alternator will supply the power to the system until the battery voltage reaches 12.7V, when the valve will close.The water will go back into drum A after it powers the alternator.
Can I wire the AC voltage from the alternator directly to AC voltage from the inverter? Do I need a battery regulator of some sorts? How can make sure I don’t blow the load and pump? Do you see any flaws or problems?
Thank You for any and all help.